Aujourd’hui, nous donnons la parole à Franck Knockaert, Responsable Industrie et Qualité chez Ciel & Terre, l’une des figures clés derrière les opérations industrielles globales de l’entreprise. Avant de plonger dans le processus de fabrication et l’expertise technique de Ciel & Terre, faisons d’abord plus ample connaissance avec Franck.
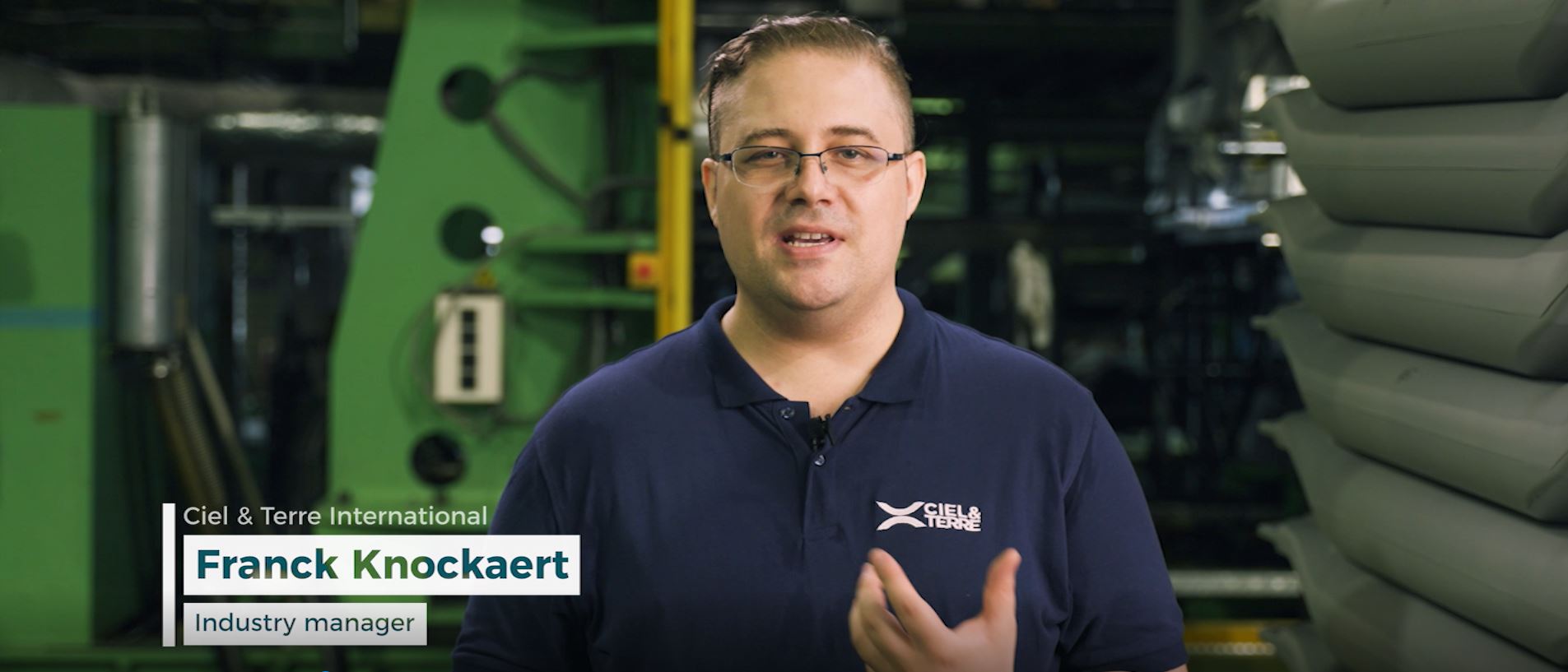
Au cœur de l’expertise industrielle du solaire flottant chez Ciel & Terre
Franck est ingénieur industriel français installé au Japon depuis plus de 10 ans. Titulaire d’un diplôme en production et logistique, il possède huit ans d’expérience dans l’industrie automobile, où il a acquis une solide expertise en optimisation des processus et assurance qualité. Il a rejoint Ciel & Terre il y a 4 ans et demi et occupe depuis janvier 2023 le poste de Responsable Industrie au niveau mondial. Son rôle est polyvalent : il accompagne les équipes industrielles et qualité à travers le groupe, en les aidant à mettre en place des processus efficaces et économiques. Il veille également à ce que les standards de qualité soient respectés tout au long de la chaîne de production. En outre, il soutient directement l’équipe R&D sur les aspects industriels et le développement de nouveaux produits. Ses responsabilités incluent aussi la création de documents de contrôle qualité et d’outils d’analyse des indicateurs clés de performance (KPI) pour les produits existants comme pour les nouveaux.
Un processus de fabrication précis pour garantir la qualité des flotteurs photovoltaïques flottants
Le fils conducteur entre fabrication industrielle et recherche & développement
En général, l’implication de la production dans le processus de R&D doit intervenir le plus tôt possible. Tandis que l’équipe R&D génère des idées innovantes, l’équipe industrielle apporte une expertise cruciale sur la faisabilité de fabrication et la maîtrise des coûts. Ainsi, les designs sont validés plus rapidement et les investissements industriels optimisés dès le départ. C’est pourquoi, la collaboration entre R&D et production favorise efficacité et innovation.
Quelles sont les étapes clés de la fabrication des flotteurs ?
Les fabricants utilisent principalement une combinaison de polyéthylène haute densité (PEHD) et de masterbatch (MB) pour créer les flotteurs par moulage par soufflage. En résumé, le processus fonctionne comme une recette, avec plusieurs étapes successives bien définies :
1- Mélange des matériaux : Tout d’abord, les opérateurs chargent un mélangeur avec les proportions précises de PEHD, de masterbatch et de regranulés (plastique recyclé).
2- Alimentation de la machine : Le mélange est ensuite transféré dans une trémie qui alimente directement une vis d’extrusion.
3- Fusion du plastique : La vis chauffe progressivement le mélange dans trois zones distinctes (alimentation, transition, fusion), atteignant environ 200°C pour rendre le plastique liquide.
4- Accumulation du plastique fondu: Une fois fondu, le plastique est transféré dans une tête d’accumulation, servant de chambre de stockage sous pression avant l’extrusion.
- Selon les machines, sa taille varie, les plus grandes pouvant stocker jusqu’à 50 litres, soit environ deux flotteurs ou près de deux fois le volume nécessaire pour un flotteur.
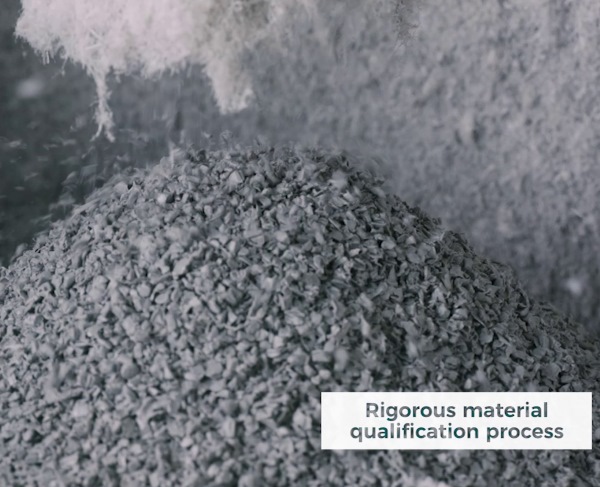

5- Formation du parison : Le plastique fondu est extrudé sous forme de tube vertical (parison), qui tombe entre les deux moitiés ouvertes du moule. Le diamètre dépend de la taille du produit.
6- Fermeture du moule et soufflage :
Lorsque le bas du parison atteint la buse de soufflage, les deux moitiés du moule se referment et pincent le tube. L’air froid est alors injecté pour gonfler le plastique à la forme du moule.
7- Refroidissement :Pendant ce temps, de l’eau froide circule dans le moule pour refroidir et solidifier le plastique. Le temps de refroidissement est strictement contrôlé pour garantir la forme et la durabilité du flotteur.
8- Démoulage : Une fois refroidi, le moule s’ouvre pour éjecter le flotteur. Celui-ci présente encore des excédents de matière sur les bords.
9- Finitions : Enfin, l’opérateur découpe les excédents et perce les trous nécessaires pour répondre aux spécifications du produit fini.
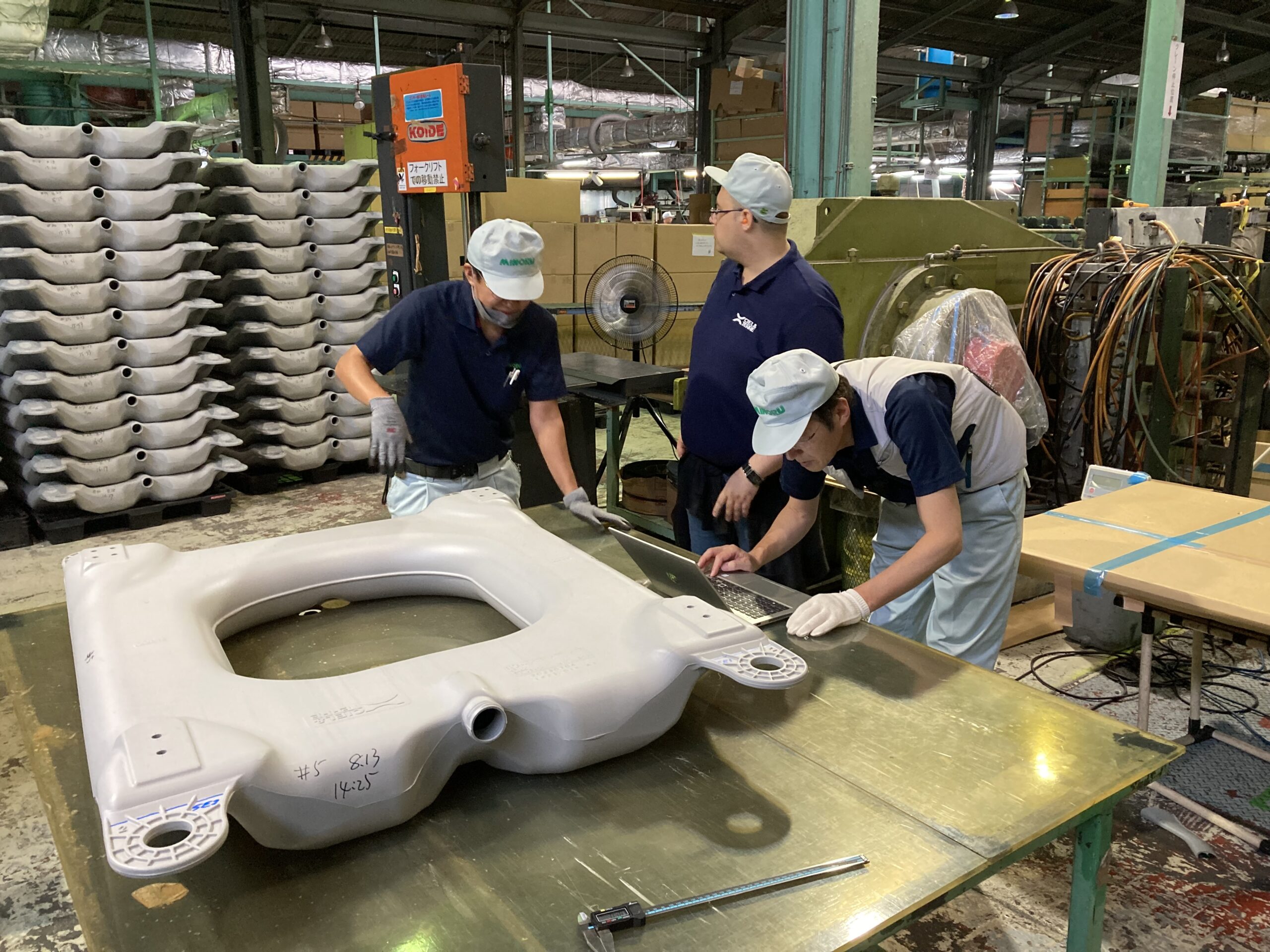
Quels sont les principaux défis pour passer du prototype de flotteur à la production finale ?
Néanmoins, le passage d’un flotteur du prototypage à la production finale présente sept défis majeurs :
- Concevoir un produit adapté au moulage par soufflage (épaisseur des parois, angles, lignes de jointure).
- Sélectionner les bons matériaux (flottabilité, solidité, résistance aux UV, etc.).
- Gérer les outils (moules, bancs de test d’étanchéité).
- Anticiper l’écart entre prototype et production de masse.
- Maintenir un contrôle qualité rigoureux à chaque étape.
- Réduire les pertes matières tout en conservant l’intégrité du produit.
- Sécuriser une chaîne d’approvisionnement fiable et stable
Comment Ciel & Terre sélectionne-t-elle ses matières premières ?
En ce qui concerne les matières premières, l’équipe chargée des achats s’occupe de l’approvisionnement. Une fois que des matériaux comme le PEHD ou le masterbatch sont validés par l’équipe R&D, nous exigeons des fournisseurs des certifications telles que le COA, la fiche technique (TDS) et les feuilles de fabrication, qui précisent la composition chimique et les propriétés mécaniques de chaque nouveau lot.
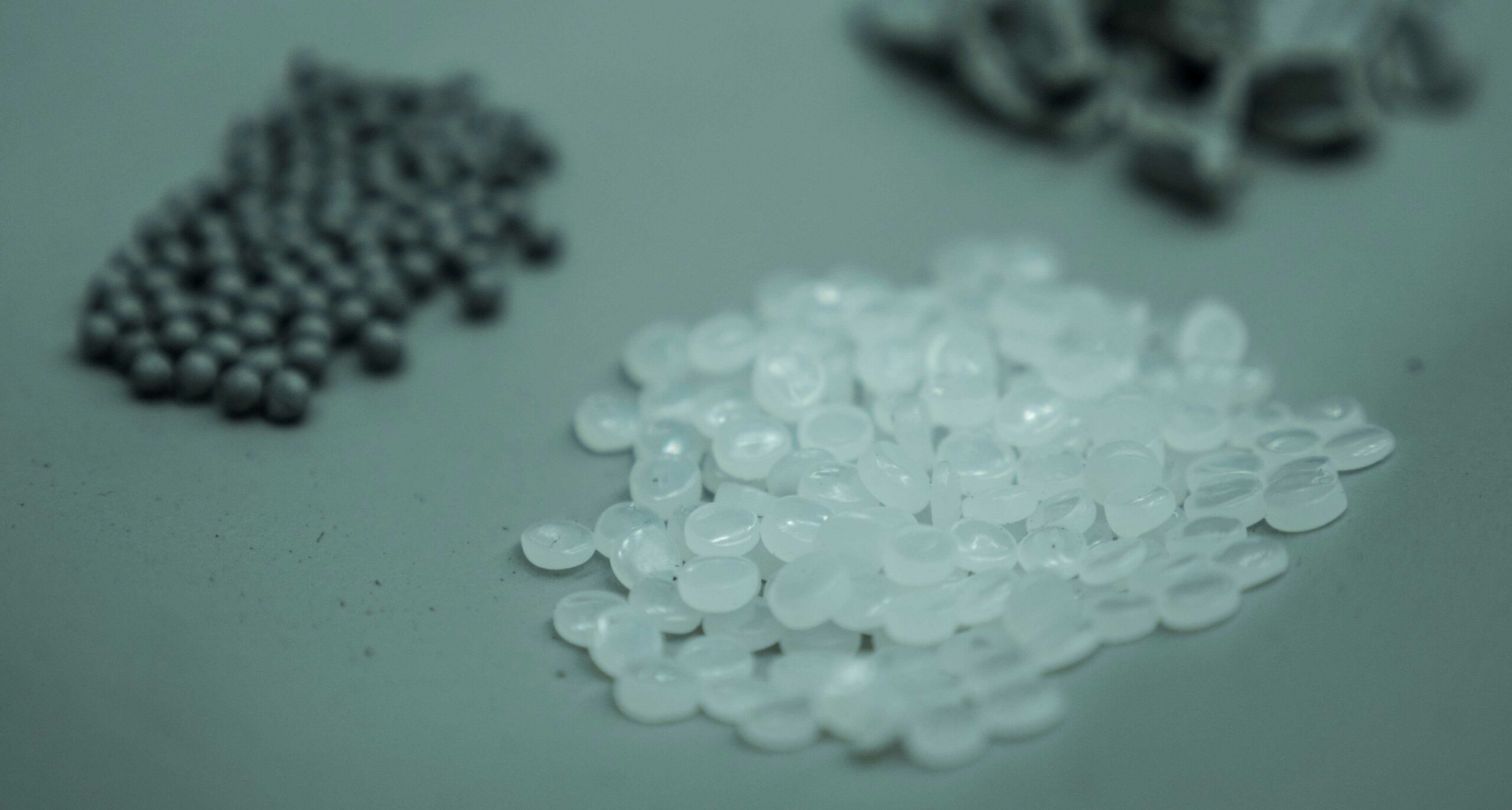
Qu’est ce que la mise en service d’un produit ?
La mise en service consiste à valider de nouveaux outils (moules) ou matériaux (masterbatch, PEHD), afin de garantir une production conforme aux plans. Les vérifications clés comprennent :
- Tout d’abord,une analyse du retrait pour anticiper le comportement dimensionnel et ajuster les gabarits de refroidissement.
- Ensuite, l’analyse dimensionnelle complète avec cartes de contrôle et analyses CP/CPK.
- Mais aussi, l’analyse de l’épaisseur pour repérer les zones critiques.
- En outre, le contrôle de la qualité de remplissage des oreilles pour assurer la résistance mécanique.
- Enfin, les inspections visuelles des zones sensibles : bouchon, lignes de séparation, logos, marquages.
Garantir la qualité tout au long du processus de fabrication
Comment Ciel & Terre assure-t-elle la qualité pendant la production ?
La qualité est garantie grâce à l’utilisation de différents outils comme :
- MSR (Management Shift Record) : rapport journalier sur le rendement, les défauts et le poids
- AFC : contrôle dimensionnel
- TFC : vérification des épaisseurs
Chacun de ces documents permettent une détection rapide des anomalies pour une correction immédiate.
Quels tests sont réalisés en usine pour garantir la fiabilité des produits ?
Avant la production, tous les opérateurs sont formés à la manipulation et à l’inspection des produits. Ils utilisent des instructions de travail, des méthodes standardisées et des checklists de défauts (defaultech) pour les guider. Pendant la production, nous effectuons :
- Des contrôles visuels (forme, date, logo, etc.)
- Des tests d’étanchéité
- Des systèmes poka-yoké pour garantir l’étanchéité du flotteur et le bon positionnement du bouchon.
Quels sont les types de défauts sur lesquels vous êtes le plus vigilant et comment les détectez-vous à temps ?
Nous sommes particulièrement vigilants face à de nombreux risques de défauts tels que l’apparition de trous, de déformations, un soufflage incomplet (miss blow), des brûlures ou encore des contaminations. Chez Ciel & Terre, nous sommes également très attentifs aux défauts les moins visibles comme : les fuites, les flotteurs en sous poids, les rayures, les excédents de matière excessifs, la circularité des bouchons, la formation de bulles ou de canaux dans les oreilles, ou encore la conformité des marquages (date de fabrication, logo etc.)
Chaque flotteur est soumis à un test d’étanchéité et à une inspection de surface avant pesée. Après des arrêts prolongés de production (plus d’une heure, week-ends, jours fériés ou lancement d’un nouveau lot), nous exigeons la validation de 5 flotteurs consécutifs conformes, incluant un contrôle de l’ébarbage des oreilles, avant de valider la reprise de la production. Ces contrôles qualité sont impératifs pour garantir un niveau de qualité constant de nos solutions solaires flottantes.
Comment gérez-vous et documentez-vous la traçabilité des matériaux tout au long de la production ?
Chaque document qualité lié aux matières premières et produits finis est soigneusement vérifié à la réception du fournisseur. La fréquence de soumission de ces documents est définie avec le fournisseur. Il en va de même pour les rapports d’analyse qualité, assurant une traçabilité complète à chaque étape de la production.
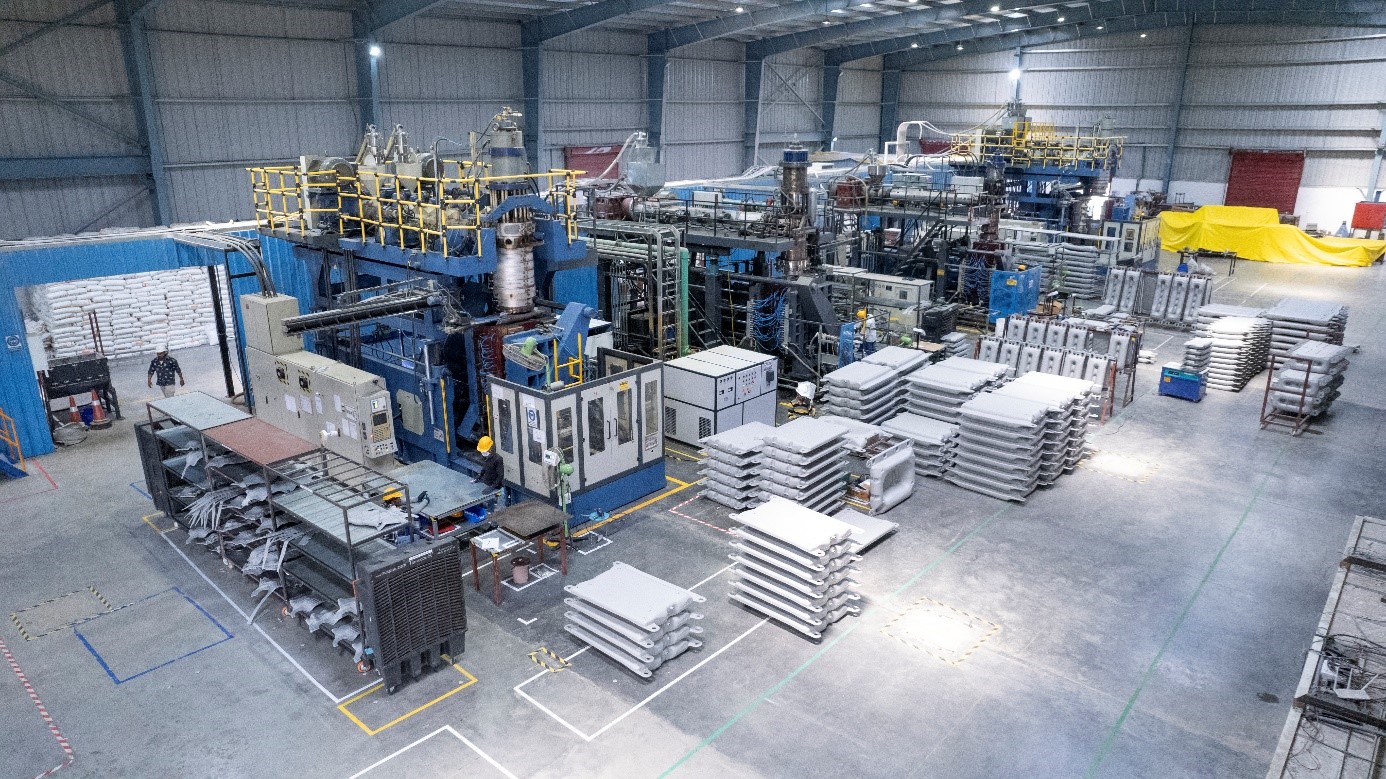
Amélioration continue et optimisation de la production
Comment optimisez-vous la production ?
Plusieurs actions contribuent à améliorer l’efficacité :
- Mise en place de la méthode 5S pour optimiser l’espace de travail sur le site de production.
- Réduction du temps de cycle et utilisation de gabarits de refroidissement pour augmenter le rendement .
- Baisse de la température de l’eau de refroidissement et augmentation du diamètre des tuyaux pour stabiliser plus rapidement les dimensions du produit.
- Positionnement du moule le plus près possible de la filière pour minimiser la longueur du parison inutile et réduire le regrind/déchets.
- Ajustement de l’épaisseur du parison selon les fichiers TCF/ACF pour rester dans les tolérances et réduire la variabilité.
- Introduction d’automatisation là où c’est viable (ébarbage, tests d’étanchéité).
- Et d’autres optimisations selon la configuration machine et les objectifs de production.
Quel est le rôle de l’automatisation et de la robotique dans vos lignes de production actuelles et futures ?
Actuellement, la plupart des partenaires disposent d’automatisations basiques telles que mélangeurs volumétriques ou gravimétriques, convoyeurs pour récupérer les rebuts, et pinces supérieures pour extraire les flotteurs du moule.
Certains sites à gros volume ont investi dans :
- Découpe automatique des bavures.
- Tests d’étanchéité automatiques.
- Gabarits de refroidissement automatisés.
Ces solutions améliorent la productivité et la constance.
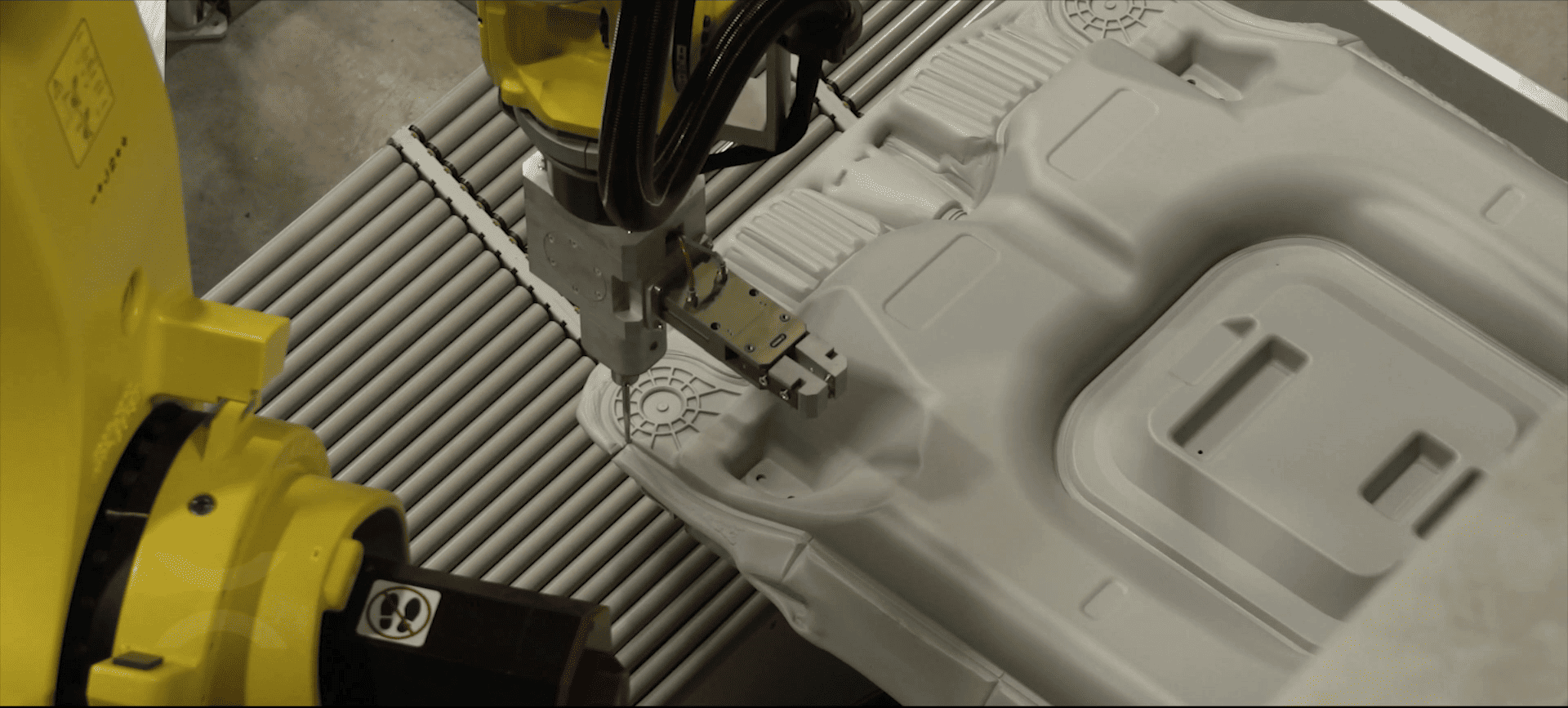
Quels processus récents ont été mis en place pour améliorer l’efficacité de la production ?
Dans notre usine en Inde, nous avons mis en œuvre avec succès la méthode 5S, incluant la délimitation de zones, les standards visuels, le marquage et des audits réguliers de nettoyage pour maintenir un espace de travail organisé et efficace.
Nous avons également collaboré avec le responsable industriel local pour optimiser le design de notre flotteur de maintenance afin de réduire la consommation de matières premières et améliorer les temps de cycle.
Quel est le délai de fabrication d’un système solaire flottant ?
Ce délai dépend de plusieurs facteurs. Un projet de 1 MW utilisant un seul type de flotteur peut être fabriqué en moins d’une semaine, voire jusqu’à 2 à 3 semaines.
Les principaux facteurs influents sont :
- Le débit de la machine de soufflage.
- La capacité de la tête d’accumulation.
- L’efficacité des tuyaux de refroidissement et de la buse de soufflage.
- La température de l’eau et de l’air.
- L’utilisation de gabarits de refroidissement externes.
- La disponibilité de plusieurs moules ou fournisseurs pour une production simultanée.
Pour un projet à grande échelle avec différents types de flotteurs et installation sur site, le planning est revu avec un chef de projet dédié qui cherchera à optimiser au mieux les temps de production.
Quels défis logistiques sont rencontrés lors du transport et de l’installation des équipements solaires flottants ?
Les principaux défis sont :
- La réglementation transport, notamment la quantité de flotteurs par palette qui varie selon les pays.
- Les limitations de taille des camions.
- Les procédures d’emballage sûres et efficaces.
- L’espace de stockage sur site, surtout dans des zones compactes comme c’est souvent le cas pour les petits étangs (exemple : Japon).
Concernant l’installation, il est recommandé de contacter l’équipe projet et construction, qui peut gérer le montage sur site en fonction de la zone géographique où se situe le projet.
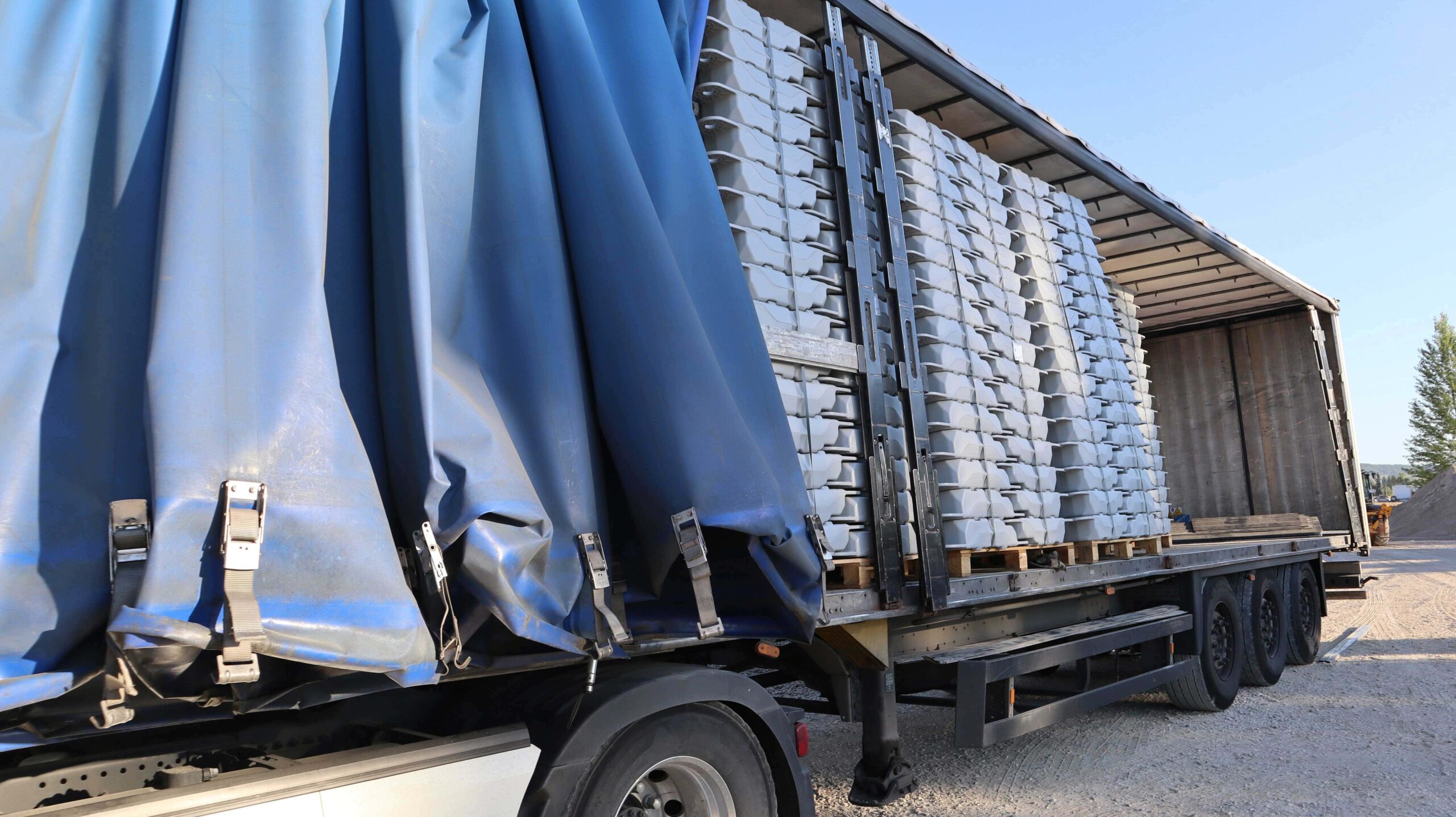
NOTRE APPROCHE MONDIALE ET CERTIFIÉE DE LA FABRICATION
Où sont fabriquées les solutions solaires flottantes de Ciel & Terre ?
Nos flotteurs sont actuellement fabriqués dans six pays : France, Japon, Taïwan, États-Unis, Inde et Brésil. Nous collaborons avec un ou plusieurs partenaires spécialisés en soufflage dans chaque pays et exploitons notre propre usine en Inde.
Comment Ciel & Terre sélectionne-t-elle ses partenaires de fabrication ?
Le choix des partenaires se fait via un processus d’audit en deux étapes :
- Un auto-audit réalisé par le fournisseur.
- Un audit sur site effectué par l’équipe Ciel & Terre.
L’audit couvre :
- La gestion de la qualité.
- La traçabilité des matières premières.
- L’amélioration continue.
- La performance de production.
- Les capacités de moules et outillages.
- Les systèmes de maintenance.
En fonction des résultats, nous évaluons l’éligibilité du fournisseur et s’il nécessite un accompagnement technique avant collaboration.
Comment l’entreprise anticipe-t-elle et s’adapte-t-elle aux évolutions réglementaires et aux certifications dans ses processus industriels ?
À ce jour, nous n’avons pas rencontré de changements majeurs de ce type. La plupart des procédés utilisés, notamment pour le soufflage, sont standards et bien établis dans l’industrie, ce qui limite l’impact des évolutions réglementaires sur nos méthodes de fabrication.
Du matériau brut au flotteur final, le processus de fabrication de Ciel & Terre repose sur la précision, la qualité et l’amélioration continue. Grâce à l’expertise de collaborateurs comme Franck Knockaert, l’entreprise garantit des solutions solaires flottantes fiables et durables, parfaitement adaptées aux enjeux énergétiques d’aujourd’hui.
PAR FRANCK , RESPONSABLE INDUSTRIE DE CIEL & TERRE JAPON
& LILOUANN, MARKETING